Fabrication de roues maison en impression 3D et polyuréthane
Trouver les « bonnes » roues pour un robot de la Coupe de France, ce n’est pas toujours facile. Pour la Coupe 2023, nous avons donc décidé de fabriquer nos propres roues. L’objectif était double:
- obtenir la meilleure intégration mécanique possible. En particulier, cette année, nous avons choisi d’utiliser des moteurs brushless, qui peuvent facilement s’intégrer à l’intérieur d’une roue creuse. L’ensemble obtenu était très compact (seulement 50mm d’épaisseur pour une roue de 35mm de large) ; la fixation de la roue au moteur était faite au moyen de vis directement dans le moyeu du moteur, sans avoir besoin d’un axe supplémentaire, et d’un système d’accouplement potentiellement fragile (les vis axiales ayant tendance à se desserrer).
- avoir une très bonne adhérence. L’adhérence des roues est en effet ce qui va limiter les accélérations du robot, mais aussi complexifier l’asservissement lorsque le robot glisse. Et l’adhérence était bien au rendez-vous, comme en témoigne cette vidéo:
Matière première: le polyuréthane
Pour choisir la matière constituant les pneus de la roue, je me suis inspiré de ce site internet, trouvé sur la maxi-liste de VRAC, qui présente la fabrication de roues pour un robot sumo. J’ai réutilisé la même gamme de matière: le Poly 74 de la marque Polytek.
Plus précisément, c’est le 74-30 que j’ai utilisé: le deuxième numéro indique la dureté (Shore) de la résine. Pour la choisir, je me suis basé sur les roues Banebot bien connues de la Coupe: celles-ci viennent en plusieurs couleurs, qui indiquent la dureté. J’avais déjà utilisé les roues blues, Shore A50, mais je les avais trouvé trop dures et donc trop peu adhérentes. La dureté la plus faible était Shore A20, ce qui est d’ailleurs utilisé sur le robot sumo du site référencé ci-dessus. Mais un robot de la Coupe de France, c’est quand même plus lourd qu’un petit sumo: il ne faudrait pas que la roue, trop souple, se déforme de facon notable sous le poids du robot, ce qui pourrait mettre en question la planéité du chassis. Nous avons donc fait le pari de prendre la dureté juste au dessus, à savoir Shore A30, et nous avons été très satisfait du résultat. Ces roues sont de loin les plus adhérentes que j’ai pu tester (nettement plus que les Banebot A50), et si la texture est un peu souple sous le doigt, le robot n’est pas assez lourd pour la déformer. A noter quand même que notre pneu est particulièrement large, 35mm: puisque le moteur rentre dans la roue et impose une certaine épaisseur, autant en profiter !
Le site de Polytek liste ses distributeurs européens ; il n’y en avait pas en France qui vende aux particuliers à l’époque, j’ai donc commandé chez Syntecshop, qui vendent le produit dans sa plus petite quantité, à savoir… 2kg (pour environ 30€) ! Sachant que notre roue (110mm de diamètre, 35mm de large, 5mm d’épaisseur de pneu) demandait environ 100g de matière, on peut en faire des roues !
Comment ca marche ? Le produit se présente sous la forme de deux liquides, sobrement appelés A et B. Pour fabriquer la résine, il suffit de mélanger ceux-ci dans les bonnes proportions (pour le Shore 30 que j’ai utilisé, 1:1), de verser le liquide dans le moule, et d’attendre tout bêtement! La réaction se fait à température ambiante sans dégagement de chaleur. Le procédé est inidiqué pour durer 16h environ ; si on est pressé la chaleur l’accélère, et il existe même un accélérateur chimique – mais pour ma part je me suis contenté d’attendre 24h avant d’ouvrir le moule. Petite note de sécurité quand même, il y a des petits pictogrammes danger sur le produit: lisez bien la notice et prenez les précautions d’usage: pièce ventilée, gants…
Fabrication d’un moule en impression 3D
L’étape la plus difficile pour la fabrication de cette roue a été de concevoir le moule. En effet, par simplicité, l’extérieur du moule est fait en impression 3D, tout comme le moyeu de la roue. Ce qui veut dire que le poyuréthane va avoir tendance à adhérer au moule autant qu’à la roue – et même plus, puisque la surface est plus grande ! Il faut donc prévoir un moule qu’on puisse assembler et démonter, sans trop forcer sur les pièces, tout en maintenant la concentricité entre le moyeu de la roue et l’anneau extérieur du moule.
Après une première tentative ratée (à base d’ergots en plastique, ce qui ne tient pas du tout la charge), notre moule ressemble à ca:
Voici les fichiers 3D (Solidworks + STL/STEP) de la roue et du moule: n’hésitez pas à vous en reservir tel quel ou comme source d’inspiration.
Comme fonctionne-t-il:
- La roue, en blue, doit être placée au centre des quatres pièces rouges formant l’extérieur du moule (découpé en 4 pour être démontable). J’ai imprimé un motif de « dents » sur le moyeu pour éviter tout risque de glissement du polyuréthane, même si vu la surface et l’adhérence, je pense qu’il n’y avait pas de risque. De même, mon pneu est texturé d’un motif : j’ai fait ca « à l’instinct », en me disant qu’avoir une surface de contact irrégulière augmenterait l’adhérence, tout en ayant un impact négligeable sur la géométrie du pneu (la texture fait 0.5mm de profondeur sur un pneu de 110mm de diamètre). Le résultat nous a convenu donc nous n’avons pas remis en question ce choix.
- Le centrage de la roue par rapport au pourtour du moule est fait grace à la plaque inférieur, dans laquelle la roue vient se visser (au niveau des trous qui seront utilisés pour l’attacher au moteur) ; les pièces externes sont tenues par des vis traversantes.
- Afin de refermer le moule, et s’assurer qu’il n’y a pas de jour entre les pièces rouges (par lesquels le polyuréthane pourrait couler, résultant en un pneu non lisse), un anneau externe orange est ajouté. La surface de celui-ci et des pièces rouges est inclinée, si bien qu’en le poussant vers le bas, les pièces rouges sont comprimées vers l’intérieur.
- Une plaque supérieure vient refermer le moule. C’est en serrant les 12 vis M4 que le moule se ferme: en conséquence, les deux plaques (supérieure et inférieure) prennent pas mal d’effort. Les notres sont en aluminium, mais je pense qu’une solution bois pourrait marcher aussi, à condition d’ajouter des rondelles. Une pièces d’interface imprimée ou un film plastique sera sans doute nécessaire pour isoler le bois, poreux, du polyuréthane. A noter que le polyuréthane adère peu à l’aluminium (trop lisse j’imagine), ce qui pour le démontage était plutôt pratique.
Cette conception du moule fait que les pièces imprimées en 3D, orange et rouge, ne travaillent qu’en compression, et ne sont donc pas abimées au cours du montage ou démontage du moule: nous avons pu utiliser le même moule pour nos 4 roues sans aucun dégats. A noter que le démoulage était quand même un peu sportif: si les deux plaques d’alu et l’anneau externe orange s’enlevaient bien (ce dernier en utilisant un serre-joint pour faire pression sur la roue tout en le bloquant par le bord, afin que les pièces rouges glissent vers le bas), le tour du moule lui-même adherait assez fortement à la roue. Polytek vend un anti-adherant, mais j’ai voulu faire sans: je me contentais de lubrifier le moule avant usage avec un spray silicone pour le rendre moins adherant (ce qui marchait un peu quand même). Pour les décoller, j’utiliais les deux trous de passage pour visser le pièce pour faire levier, puis je basculais le quart de cercle vers l’extérieur. Le polyuréthane a une structure elastique mais est très difficile à déchirer, si bien que même s’il me fallait pas mal forcer, et que la séparation s’accompagnait d’un bruit de suction horrible laissant présager le pire, en pratique l’état de surface de la pièce comme du moule était nickel: je retrouvais toutes les petites textures de 1mm sans rien qui reste accroché dans le moule.
Malgré la présence de moult vis, le moule n’était pas tout à fait hermétique, et une partie du liquide finissait par couler. Sur mes premières roues, le pneu était ainsi environ 2mm plus court que le moyeu de la roue. Pour contrer cet effet, j’ai ensuite rajouté un simple cercle imprimé en 3D du même diamètre que le moyeu de la roue, au dessus de celui-ci: ceci me permetait de remplir le moule au dela de la taille du moyeu, compensant la perte de matière (avec un bon coup de scalpel ensuite pour enlever l’excédent).
Conclusion
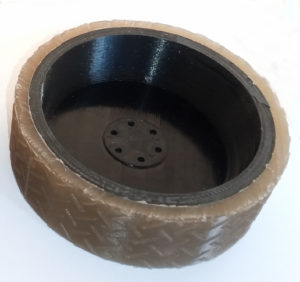
Une roue terminée. La coleur matte est la teinte naturelle du polyuréthane, mais il est possible d’ajouter des pigments.
Nous avons été très satisfaits de cette expérience de fabrication de roue. Il faut accorder un peu de réflexion à la fabrication du moule ; notre premier prototype, à base d’ergot imprimés en 3D, n’a pas résisté bien longtemps à nos efforts pour l’ouvrir. Il faut compter sur une forte adhérence du polyuréthane au PLA ; l’utilisation de l’agent de démoulage officiel aiderait peut-être.
Une fois le moule créé, la fabrication en elle-même était toute simple: mélanger les deux liquides, les verser dans le moule, l’agiter un peu pour que ca se stabilise et pour faire partir d’éventuelles bulles (à noter qu’il restait toujours des micros-bulles en suspension, mais celle-ci semblent disparaitre au cours du séchage – en tout cas elles ne sont pas visibles sur la surface de la roue, et donc ne nous gènent pas), et attendre 24h. Le résultat est une très bonne intégration mécanique, et une exellente adhérence, comme démontré dans la vidéo. A vrai dire, ce niveau d’adhérence est probablement « overkill » – en tout cas cette année, nous étions loin d’atteindre de telles valeurs d’accélérations. Mais ca reste très satifaisant de se dire qu’on a su fabriquer une roue sur mesure !